
The drag-enabled interface lets you visually define how much displacement you’ll permit in the design.įor those with multicore workstations, Inspire lets you specify the number of cores you want to deploy to solve the optimization.

The displacement constraint setup dialog box allows you to use to set deflection value.
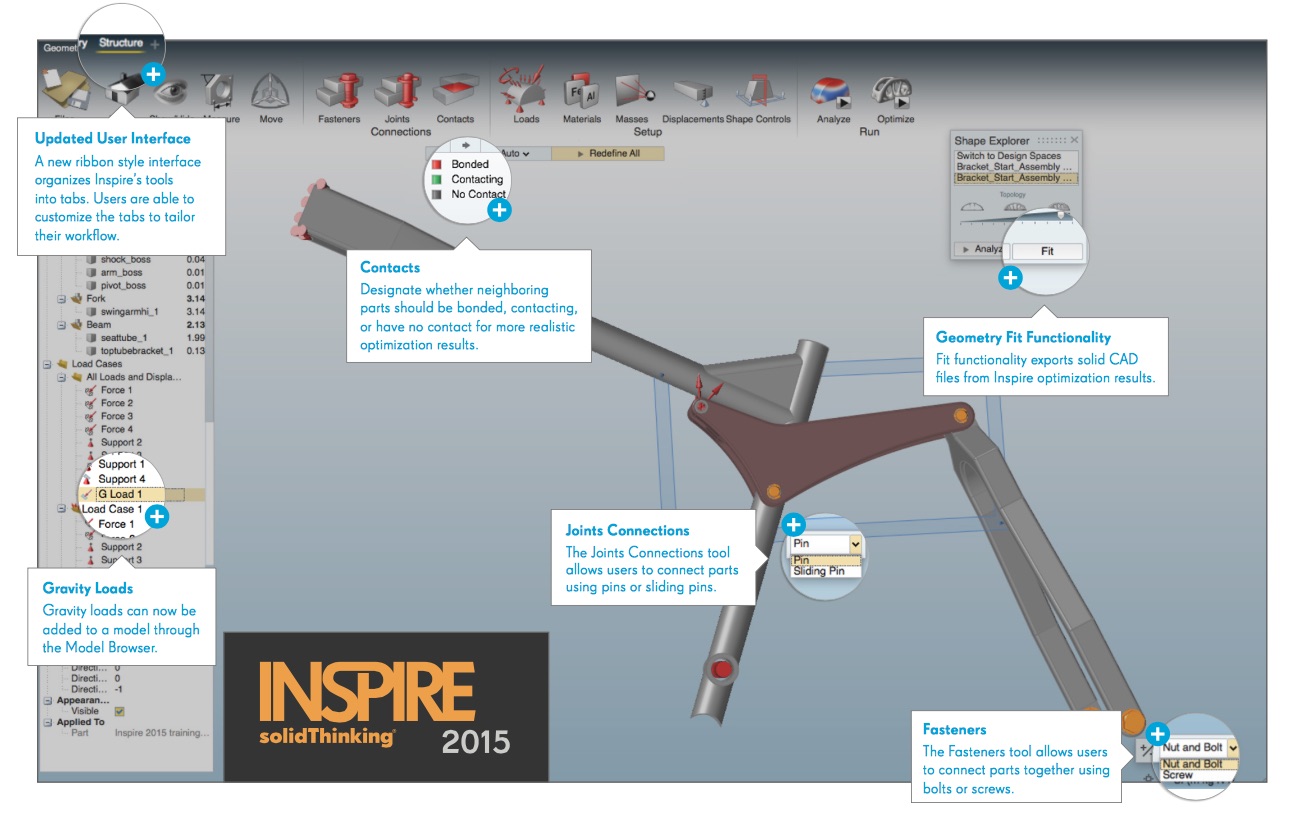
In addition to the option “minimize mass,” you’ll have the option “maximize stiffness.” Other options in the optimization dialog box allow you to set frequency limit (the rate at which the design vibrates) or thickness.
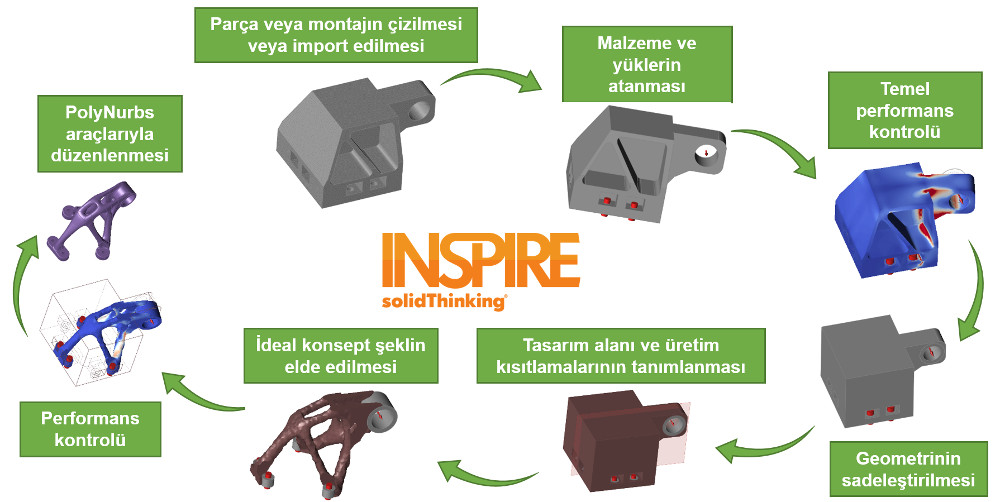
That’s one of the improvements included in the new version of Inspire, Altair’s optimization software targeting designers.Īlso in the new version is the ability to optimize for desired stiffness. If you have entered a safety factor that the design cannot physically accommodate (perhaps because there just isn’t enough materials to trim to get to the desired results), you’ll know. In Altair’s SolidThinking Inspire 9.5, when computation fails during an optimization session, you’d have the option to open up the Violation Table and inspect several columns of listed reasons. You can’t initiate a postmortem analysis, like you would with a real person, by asking, “Why can’t you compute that scenario? What happened?” It behooves you to know, because in that unexplained failure is a nugget of wisdom that may reveal something about your design’s weakness. The frustrating part about this process is, you can’t communicate with the software. Or it displays the dreaded exclamation point embedded in a yellow triangle (software speak for “You’ve messed up!). Just to start off the process, the user might plug in a safety factor that seems reasonable. And that can be a stumbling block for some users, especially if they’re not simulation experts, or if the design is still at an experimental concept phase. If you want the software to come up with the best possible shape build with the least amount of plastic to withstand a certain force, you need to tell the software what that force is.
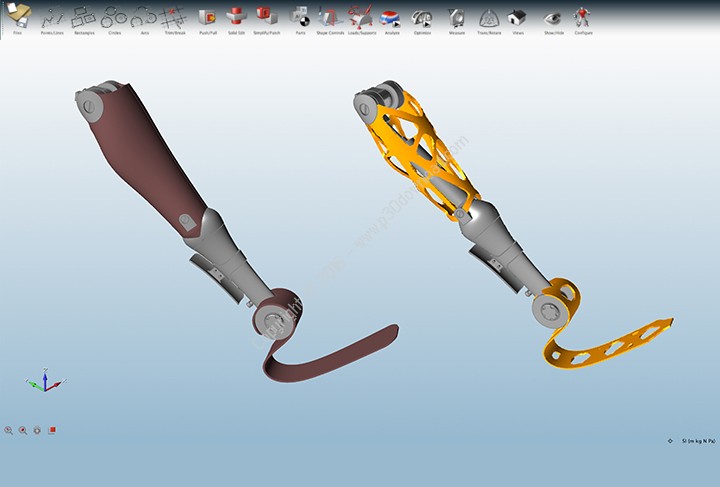
Optimization exercises are driven by input parameters- your inputs.
